Construction is fast, physical, and constantly in motion. But until recently, documentation lagged behind – scattered photos, handwritten as-builts and manual markups that left too much open to interpretation.
That’s no longer the case.
Reality capture technology is redefining how the construction industry captures progress, tracks changes, and collaborates across the project lifecycle. Using advanced tools like drones, laser scanners, 360° cameras, and LiDAR, project teams can generate accurate, up-to-date digital records of their construction sites – turning site conditions into measurable models that align everyone from field to office.
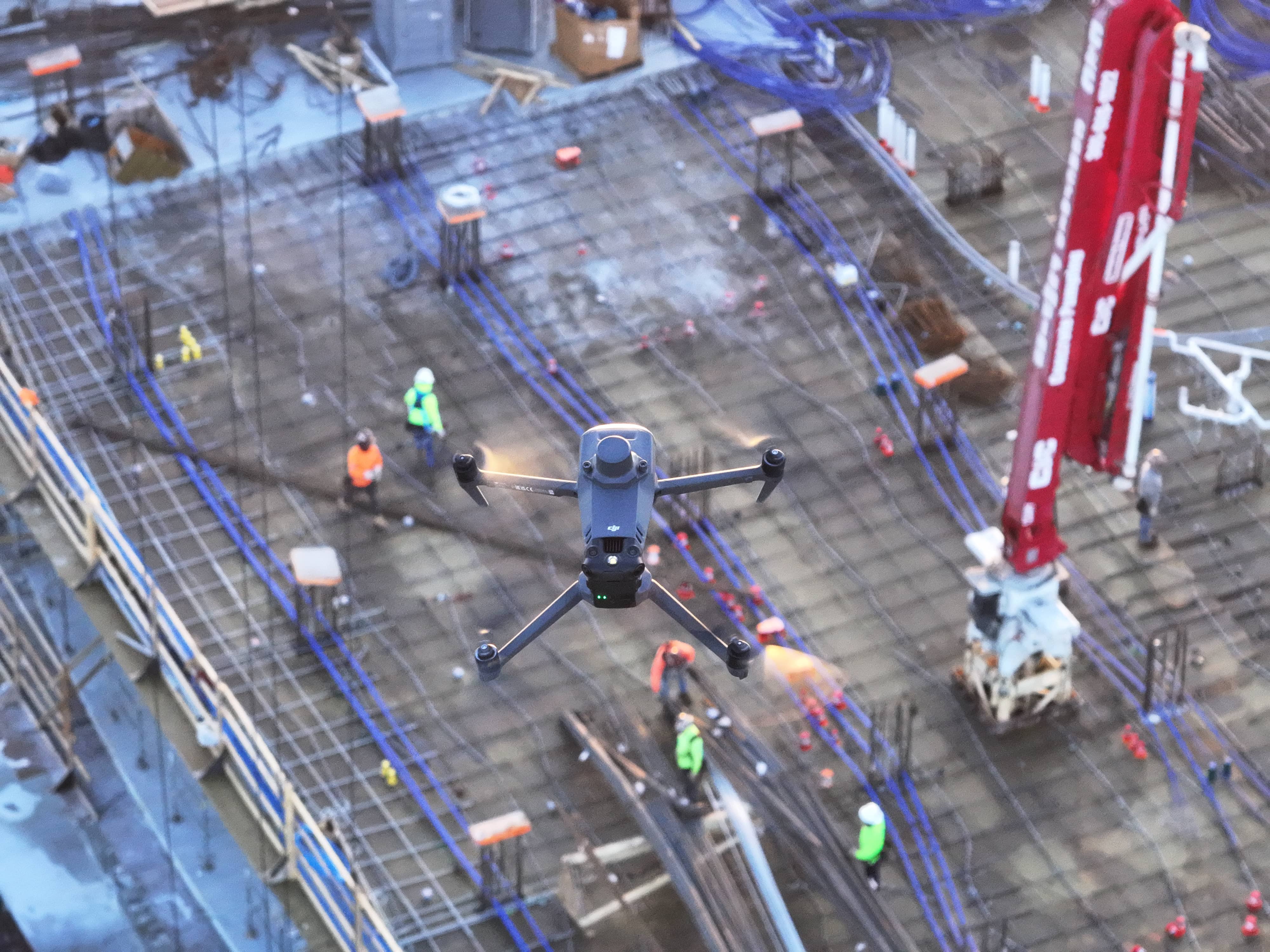
What is reality capture in construction?
Reality capture in construction refers to digitally documenting physical environments to produce 3D site models, orthomosaics or as-built data. It replaces fragmented workflows with a single source of truth—one that’s visual, timestamped, and measurable.
Using tools like:
- UAV photogrammetry (drone maps)
- 360-degree walkthroughs
- LiDAR and 3D laser scanning
Teams can create digital models of buildings, structures, and infrastructure that reflect real-world conditions at any phase of a construction project.
The result? Better visibility. Better coordination. Fewer surprises.
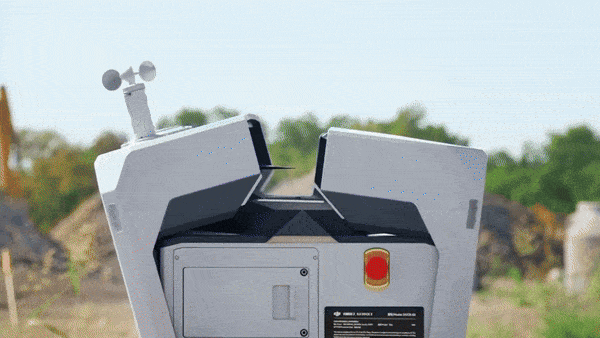
From manual workflows to measurable models
Most construction professionals have lived the pain of missing or outdated documentation. A pipe gets covered before inspection. A sleeve gets moved but not noted. By the time it’s discovered, it’s too late.
That’s why construction workflows are shifting toward reality capture solutions.
Today’s best teams use 3D reality capture to generate as-built models that sync directly with their design model, schedule, and coordination tools. The workflow is faster, the data is centralized, and everyone – from the design team to the foreman – works off the same playbook.
Discover how DPR is transforming the way they build with reality capture:
Why reality capture matters now
Deadlines are tight. Budgets are tighter. And the demand for transparency is higher than ever.
Reality capture technology helps construction companies navigate all three.
It reduces the need for repeated site visits by providing remote, real-time views of current conditions. It improves risk management by flagging issues early. And it provides verifiable, accurate documentation for every major install, pour, or inspection—without adding friction to the jobsite.
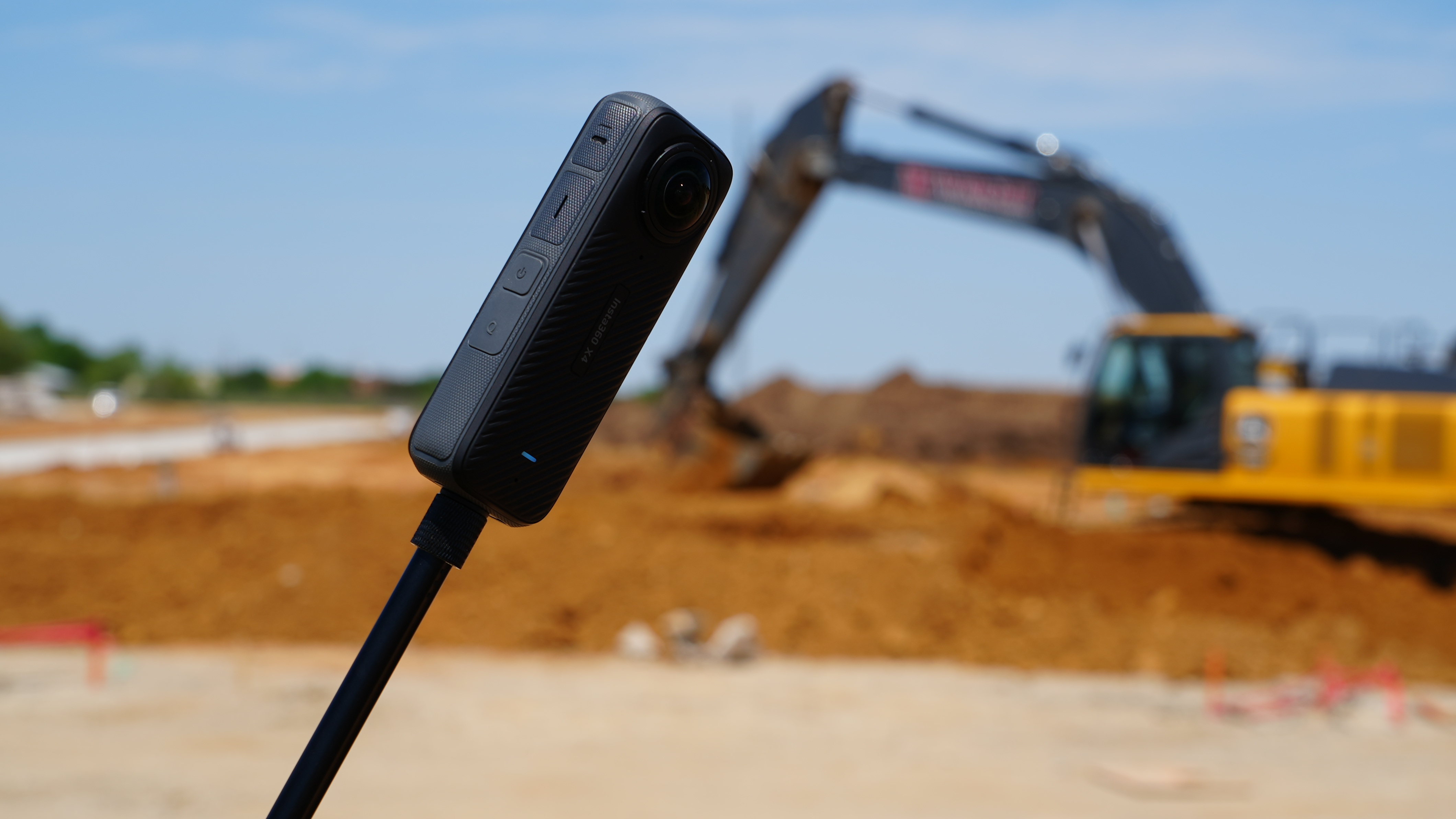
More than photos: a shared source of truth
In the context of construction, misalignment between teams often comes from one thing: missing or outdated site data.
Reality capture closes that gap.
By combining laser scanning, aerial images, and 360-degree walkthroughs into one platform, teams get a central source of visual truth. Whether it’s an owner reviewing the mechanical room from a different state or a PM verifying work before an OAC meeting, everyone has access to the same, trusted visuals.
The benefits of construction reality capture
Let’s talk about outcomes:
Reality capture enables:
- Fewer RFIs, because you’ve already got the visual reference
- Smoother inspections, with accurate as-built information always on hand
- Reduced rework, thanks to early issue detection and comparison tools
- Clearer documentation, with a searchable archive of every phase of work
From asset maintenance to cost savings, the benefits of reality capture show up across the entire project timeline.
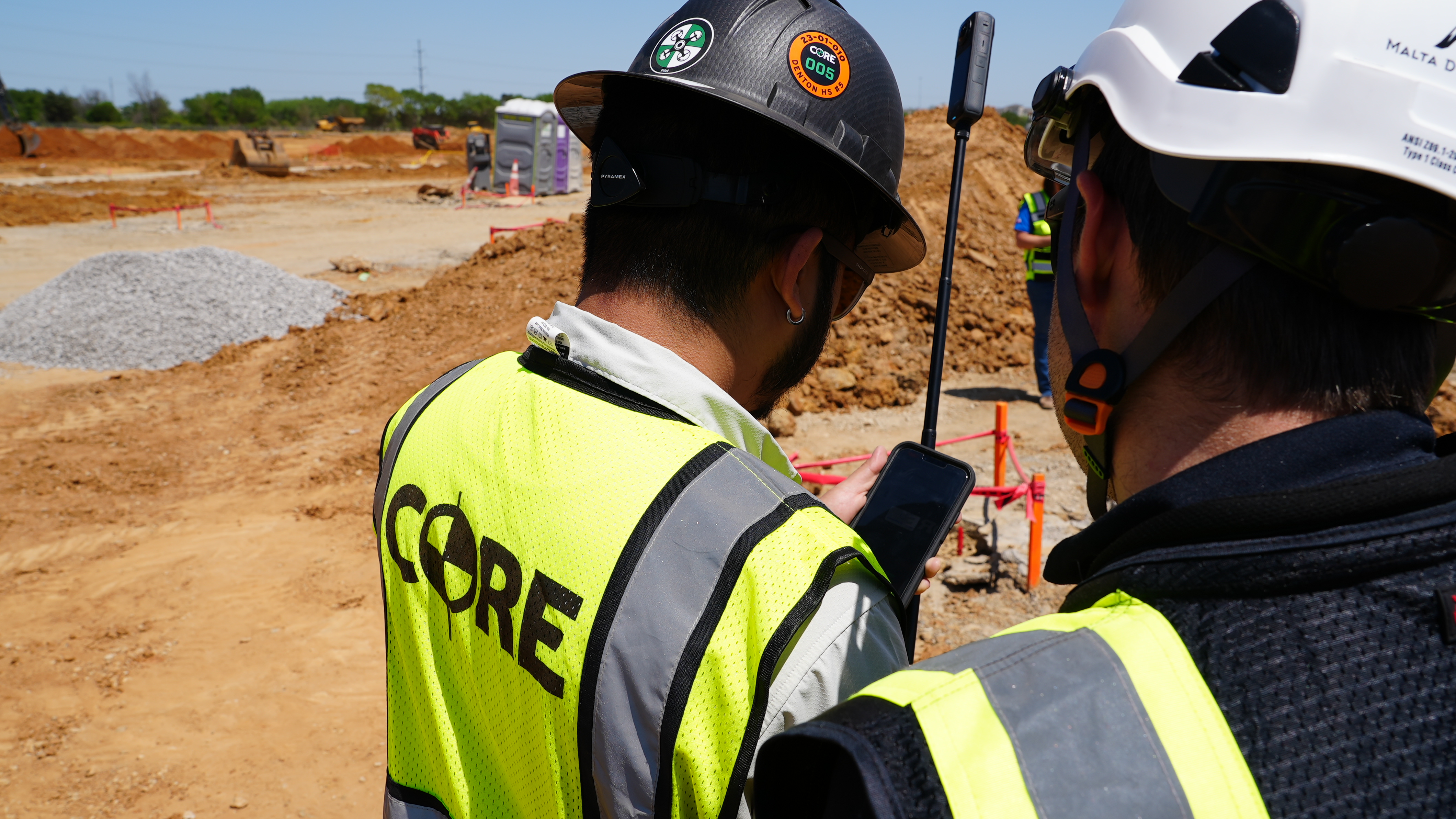
360-degree cameras: fast, reliable, and field-ready
For interior spaces, 360 cameras offer fast and easy capture without requiring a drone or scanner.
In just a few minutes, field teams can create immersive walkthroughs of hallways, units, or mechanical spaces. That footage becomes a searchable, navigable digital model that’s synced to the floor plan and accessible from anywhere.
It’s a simple yet powerful tool for improving coordination, reducing destructive investigations, and maintaining as-built documentation as walls go up.
Drone mapping: the scalable eye in the sky
When it comes to civil construction or large jobsite coverage, drone mapping delivers fast, safe, and scalable visibility.
With just one flight, teams can generate detailed 3D models of construction sites using photogrammetry, enabling volume calculations, accurate estimates, and high-resolution site progress reports.
These scans integrate directly into platforms like Autodesk Construction Cloud, supporting construction collaboration across disciplines.
LiDAR and scan-to-BIM: precision where it counts
For projects that require accurate as-built models, such as MEP retrofits, tight-tolerance installs, or facade coordination, LiDAR provides the precision you can’t get from photos alone.
Laser scanning captures dense point clouds of physical environments, which can be translated into a federated model or overlaid onto your design model for comparison. This is especially valuable in complex builds or high-stakes commercial and heavy construction industry work.
Incorporate tools like the Leica BLK2GO PULSE First-Person Scanner or Reality Cloud Studio to automate even further.
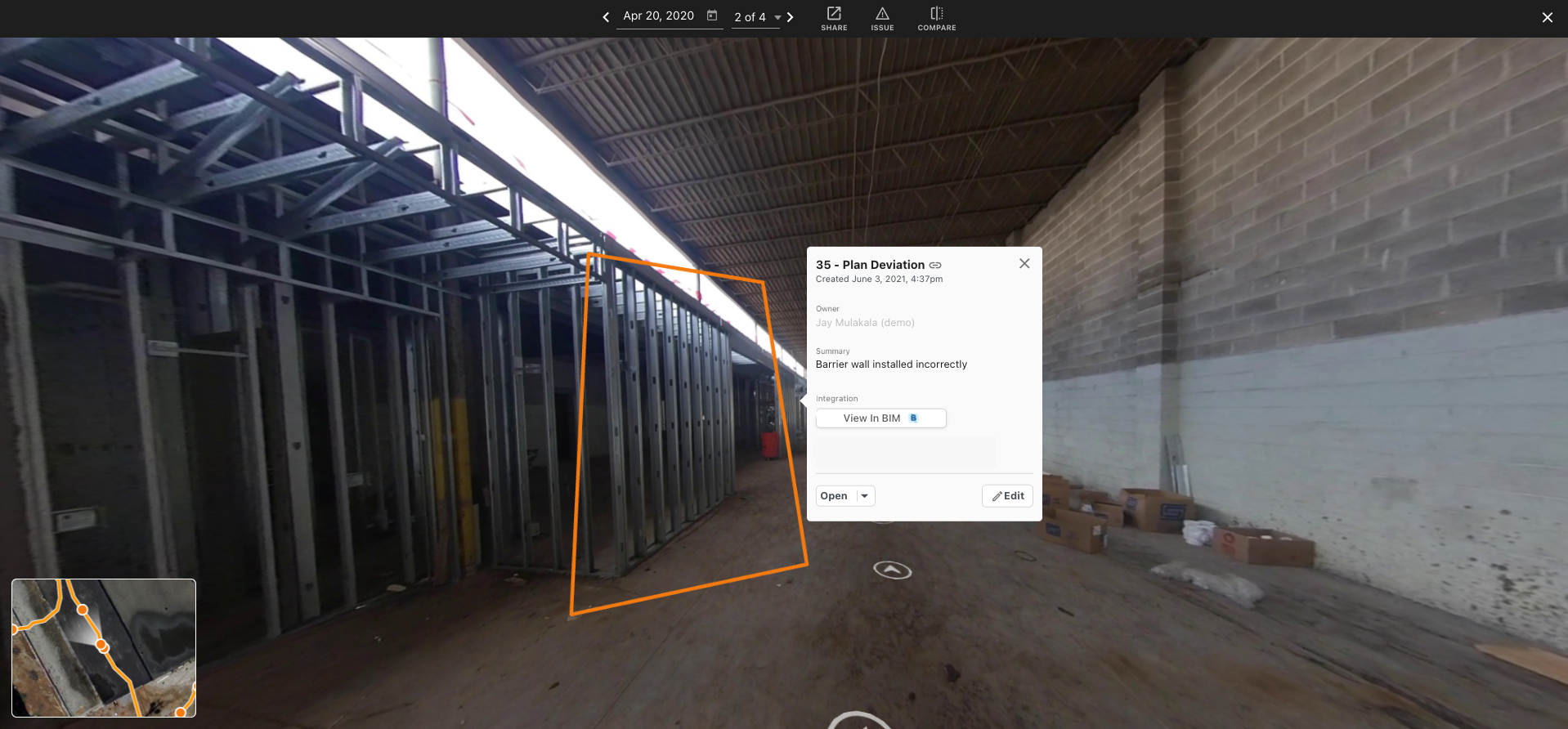
Integrated workflows with BIM and PM tools
The power of reality capture grows when it connects to the systems your team already uses.
Reality capture data can be tied to RFIs, linked to drawings, or compared directly within tools like Autodesk Construction Cloud, Procore, or other asset management platforms. That means faster approvals, fewer miscommunications, and more informed decisions – right where they’re needed.
It’s the foundation of connected, data-driven decisions in modern construction technology.
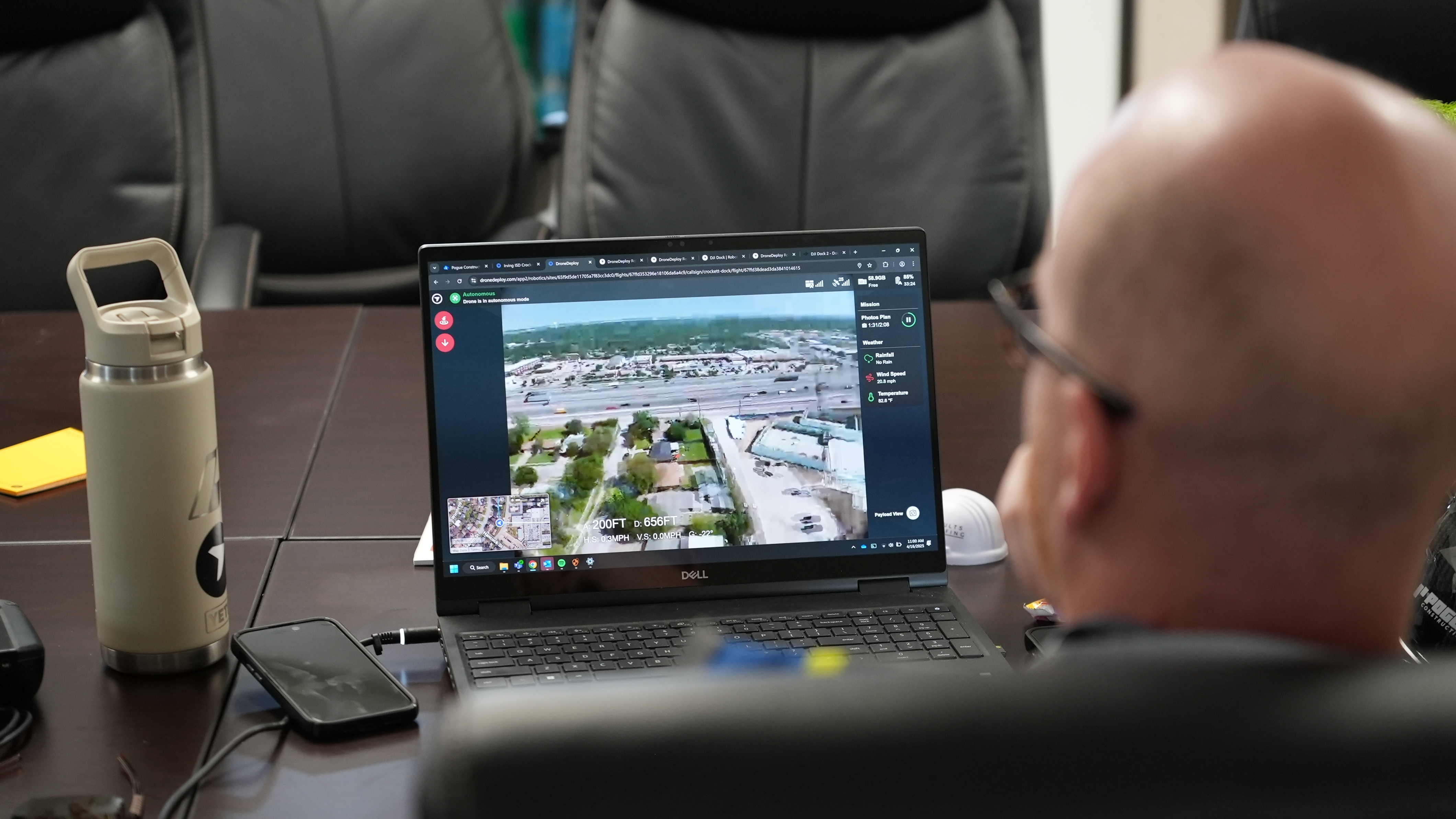
Data without the overwhelm
Yes, capture creates a lot of data. But smart platforms simplify the collection process.
Reality capture software organizes and geolocates files, connects them to relevant plans, and ensures your construction teams are only seeing what matters – whether it’s as-build information for a closeout package or current visuals for a trade walkthrough.
When your visuals are streamlined, your workflows follow.
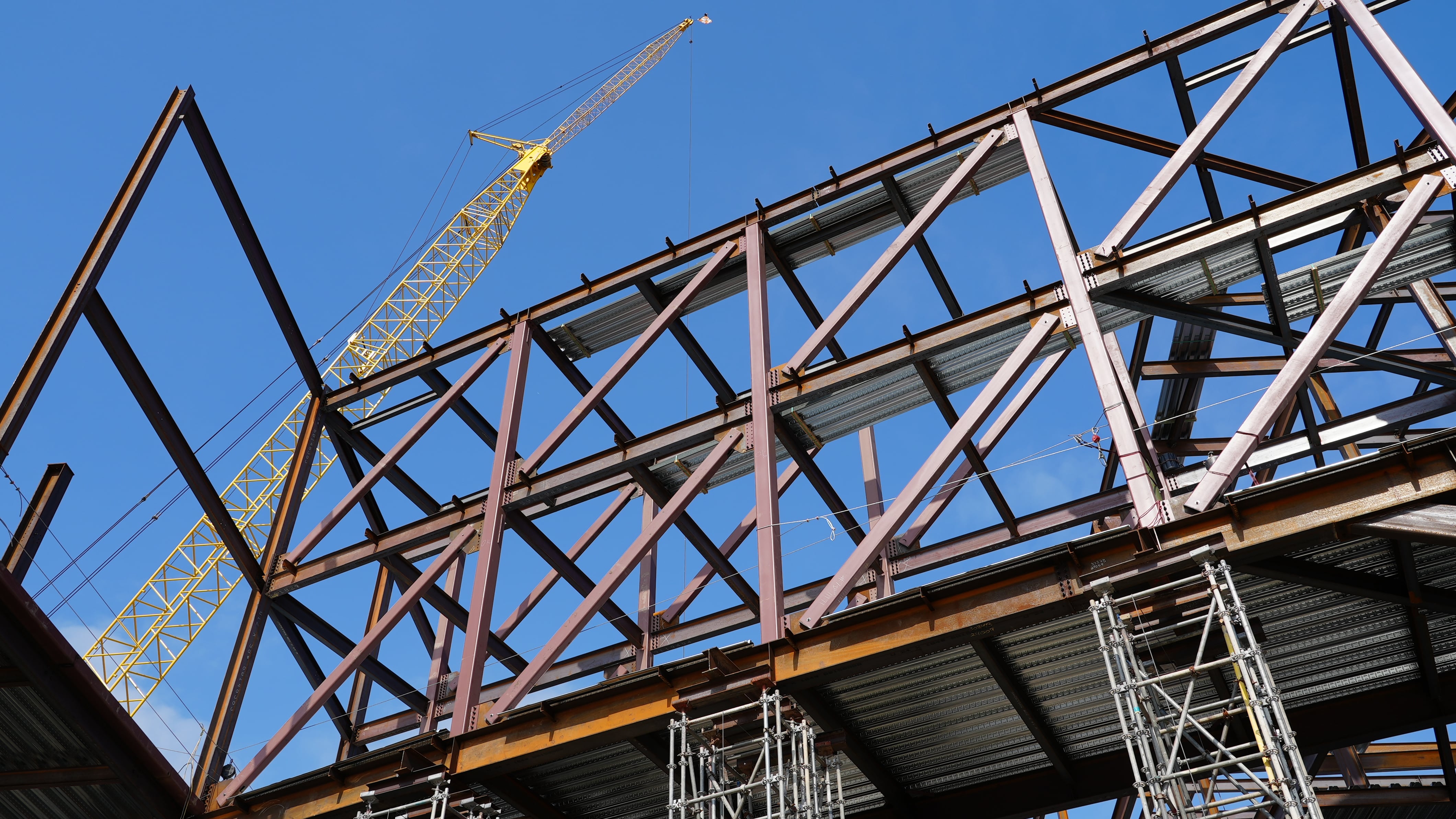
Assigning ownership: who drives capture success?
The best capture workflows don’t run themselves – they’re owned by someone on the ground.
Whether it’s a VDC manager, project engineer, or superintendent, the right person can champion the reality capture workflows, train others and ensure the construction data analytics coming from the field is reliable and standardized.
When capture is consistent, it becomes part of the process – not another line item to check off.
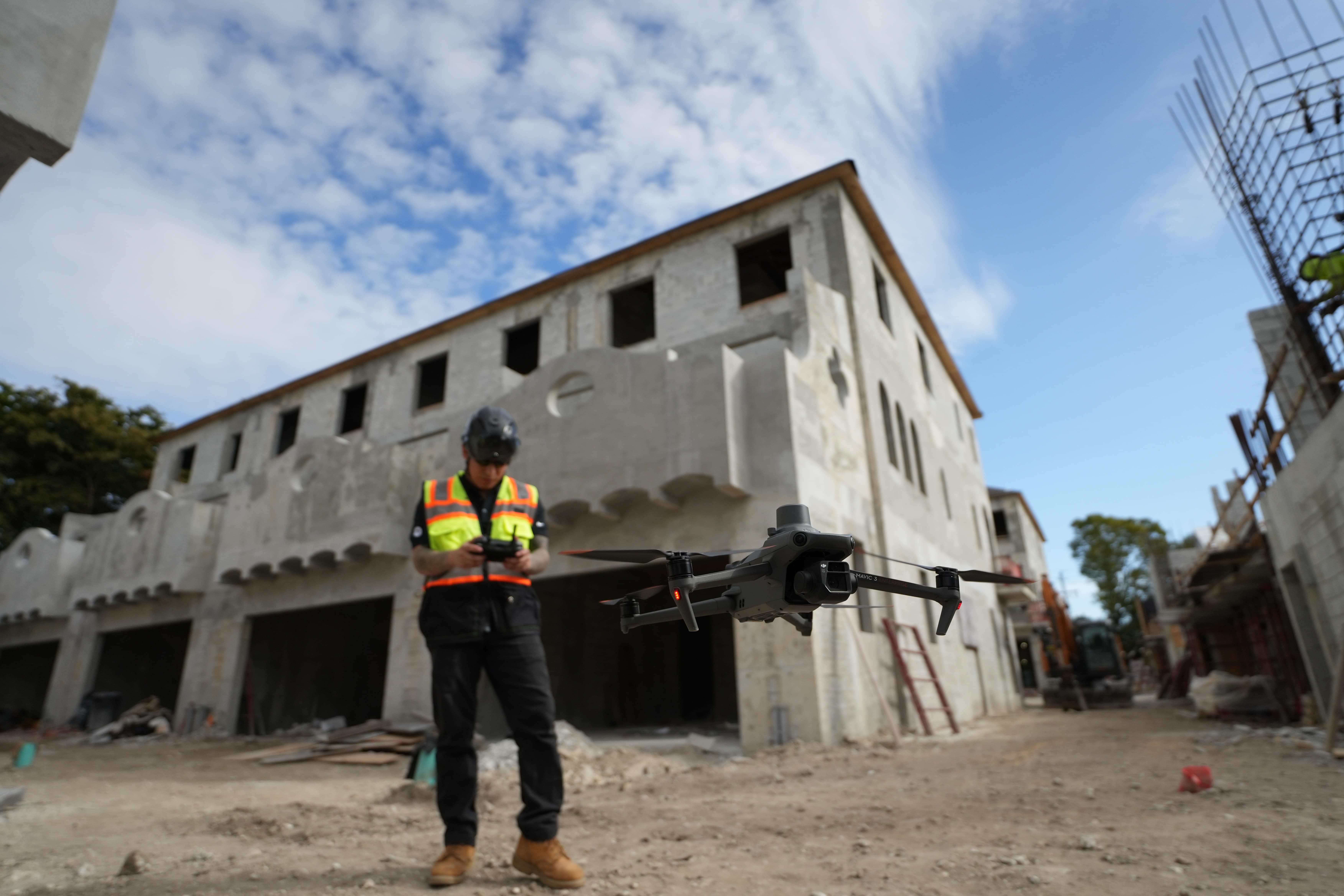
Overcoming resistance to new tools
Adoption doesn’t happen by accident. It happens when teams see value – fast.
Start with one pilot site. Focus on capturing key milestones, using workflows that mirror current practice. Integrate with tools they already know. And most importantly, tie wins back to real outcomes: saved time, reduced risk, fewer delays.
Once teams experience the power of reality capture, it sells itself.
What’s next in construction reality capture?
This technology is just getting started.
Autonomous flying laser scanners, AI-powered issue detection, and hands-free jobsite capture are all on the horizon. More firms are embedding these workflows across portfolios, from earthwork operations to closeout.
The future of construction processes is visual, measurable, and model-driven. If you're not building with capture in mind, you're building blind.
Learn everything you need to know about reality capture in construction:
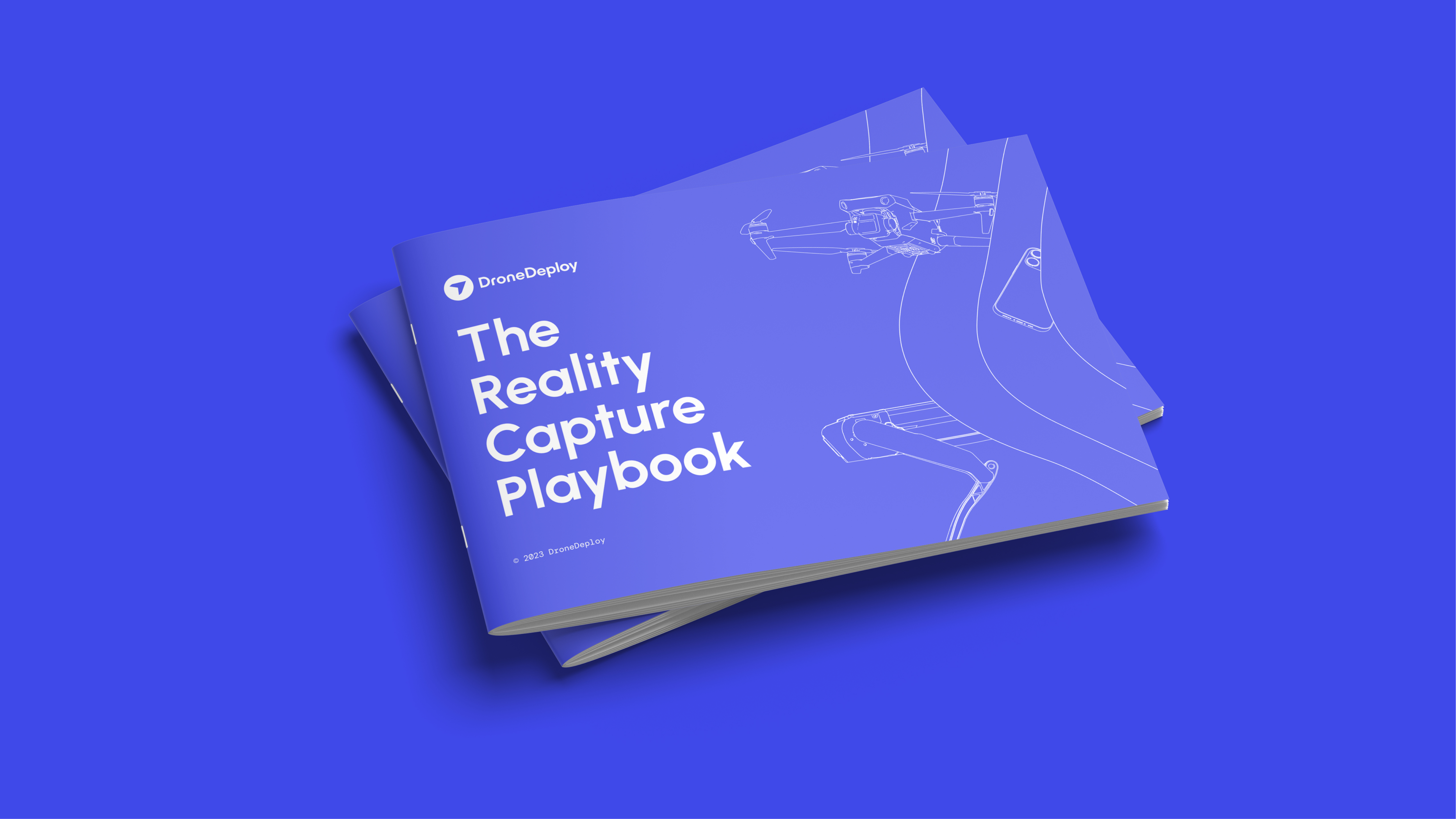
Capture with confidence
Reality capture has become the foundation of modern construction workflows. It gives teams clarity, accuracy, and control over how projects are documented, tracked, and delivered.
By turning jobsite conditions into digital records, it empowers every stakeholder to make informed decisions, protect margins, and keep the project moving—no matter where they are.
The firms who adopt early? They’re not just documenting the jobsite. They’re redefining how we build.
Ready to see it for yourself? Get in touch with our team.